Two Means to Two Ends: Digital Fabrication in Coture Fashion and Food
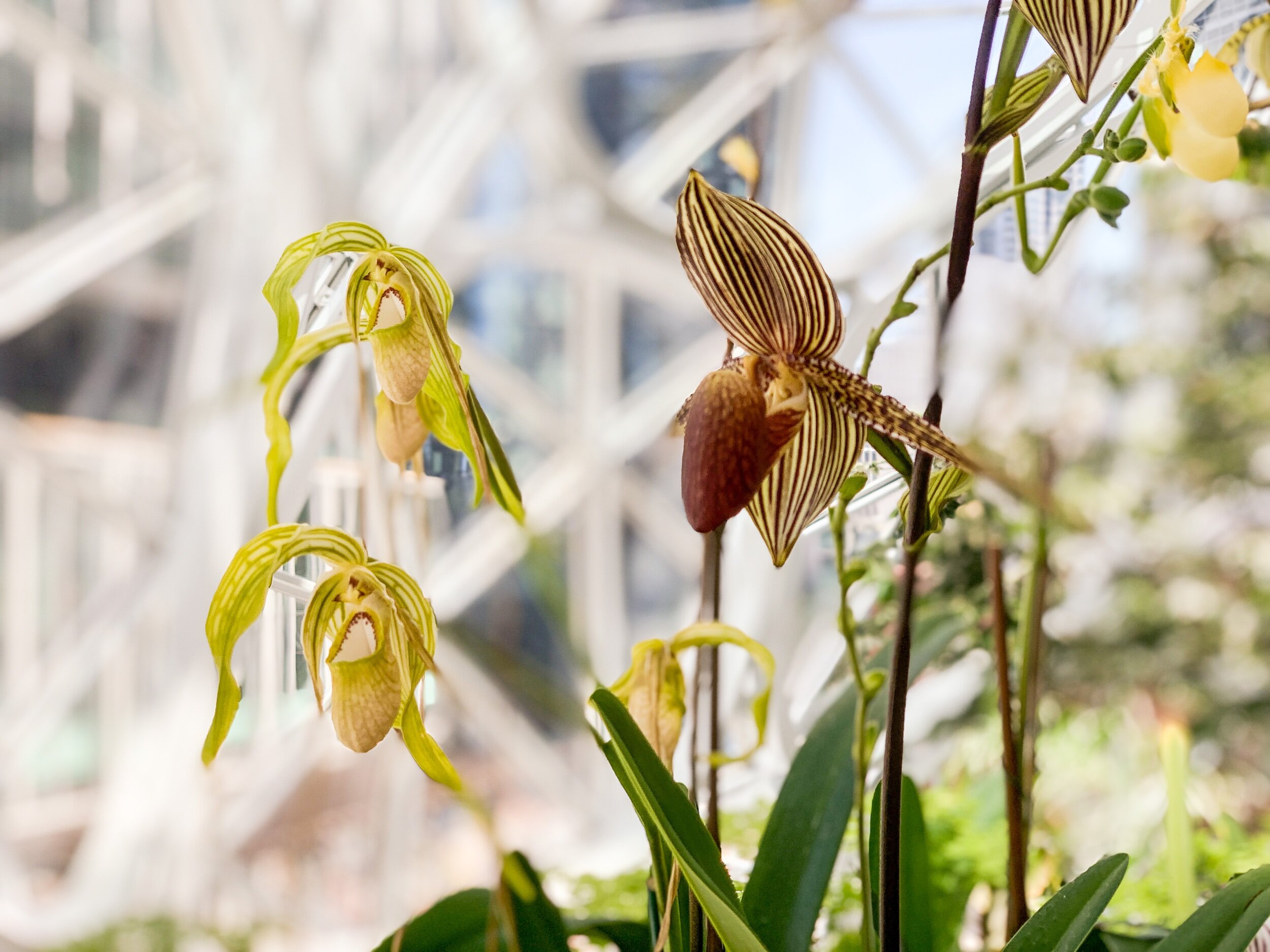
Remember that one time when I thought this would be a weekly thing? Perhaps this will be re-christened Monthly, Semi-Annual Digest, or Whenever-The-Mood-Strikes Digest. For the moment, A Digest will suffice.
Iris Van Herpen’s work is captivating and exhilarating. I love the integration of the built environment - a tremendous, kinetic installation by Studio Drift floating over the catwalk - with the runway show for Fall 2018 Paris Fashion Week’s Syntopia show, and have watched this video on repeat. Her studio’s Instagram shows behind the scenes peeks into the extensive fabrication process that takes place to produce the elaborate garments. Fabric and color, suspended taut over shapely wire armatures, are layered in myriad, repetitive ways. Lush, pleated fabric ripples effortlessly, and seems to take on a life and motion of its own when the wearer moves ever so slightly. I am not sure which draws me in more - the pieces with heavily contrasted piping, or the ones where the fabric is a blur of color. Both are riveting.
Because more creative fabrication is better and creative fabrication when applied to dessert is best, I am this mesmerizing video of self-taught pasty chef and architect Dinara Kasko using a 3-D printed mold to make a cherry layer cake. The first steps of her process are very similar to the ones used in architecture school to make models:
Design. Build a three dimensional model of the “positive” or “solid” portion of the design (the design and 3D model parts are often very much integrated). The idea of a positive and a negative, or even “solid” and “void” idea will be unpacked below.
Simplify and adjust to make it printable. (Many 3D printers have a low resolution defined by the type and thickness of the output material.)
Translate into the 3D printer program. (Many current printers can now receive direct output from popular modeling programs such as Rhino - during grad school a whopping decade ago this was not the case.)
Print. Frequently, this takes multiple iterations as the filament is not always printed properly or prints sloppily, the direction of printing may look better in when rotated, scale can be increased or decreased, honeycombing may be exposed, or filament can run out! The printing itself also takes a long time. Also, models that exceed the size of the 3D printer bed are designed to be printed in multiple pieces.
Cast the 3D printed model - the positive or solid part of the design - in a silicone rubber to create a mold. Dragon Skin is frequently used. Poured in as a liquid, it fills around every nook and cranny to create an inverted replica - the negative or the void - of the design. Once the mold is set, it can be peeled away from the printed model, and used to easily cast the design in different materials - resins, concrete, etc. for architectural models or chocolate mousse if you are Kasko.
Read more about Kasko here, or check out her Instagram - do not be surprised when you are sucked in to the incredible photos and videos of cakes and bonbons delicately prepared, assembled, and presented. Slices are shown of the layered assemblies almost as architectural sections. Not only is her work beautiful and rigorous in its execution, but apparently her patisserie is delicious as well, as she is committed not only to exploring beauty in angles and sugar, but also to the use of excellent ingredients.